ترکیب فولاد ضد زنگ برای بسیاری از کاربردها که در آن استحکام، مقاومت در برابر خوردگی و کیفیت سطح اهمیت دارد یک مورد کلیدی است. اما دقیقاً چه چیزی باعث می شود که فولاد ضد زنگ محافظت و جذابیت زیبایی را که ما انتظارش را داریم ارائه دهد؟
جالب است بدانید که در هر نوع فولاد آلیاژی ضد زنگ حداقل حاوی 10.5٪ کروم است. ترکیب فولاد ضد زنگ ممکن است شامل کربن، سیلیکون، منگنز، فسفر، گوگرد، نیکل، مولیبدن و تیتانیوم باشد.
هر یک از این عناصر ویژگی خاصی از فولاد آلیاژی را تقویت می کند. انواع مختلف فولاد ضد زنگ در شکل های مختلف از جمله ورق فولاد ضد زنگ، میلگرد ضد زنگ و لوله استنلس استیل تولید می شود، ترکیبات منیفولد فولاد ضد زنگ منجر به فهرست گسترده ای ازمحصولات می شود.
فولاد آلیاژی چه ویژگی های خاصی را دارد؟
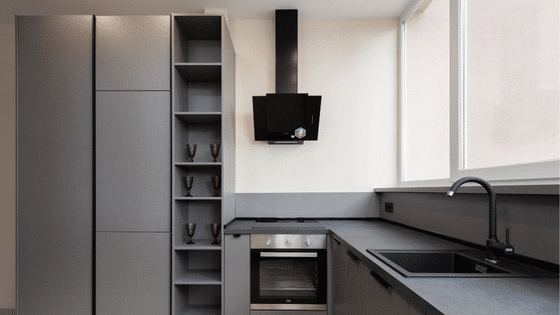
خواصی که برخی عناصر آلیاژی بهبود می بخشند عبارتند از: چقرمگی، مغناطیس، استحکام، مقاومت در برابر خوردگی، مقاومت در برابر تنش، دوام، کارایی و قابلیت عملیات حرارتی.
با بیش از 150 گرید مختلف موجود از فولاد ضد زنگ، تغییرات در ترکیب منجر به ویژگی های مختلف و منحصر بفرد می شود.
ترکیبات فولاد ضد زنگ چیست؟
نسبت فلزاتی که آلیاژ را تشکیل می دهند تعیین می کند که درجه فولاد ضد زنگ به کدام خانواده تعلق دارد. درک پنج خانواده مختلف فولاد زنگ نزن – آستنیتی، فریتی، آستنیتی-فریتی (دوبلکس)، مارتنزیتی، و سخت شده در اثر بارش- یکی از راههای به یاد آوردن چگونگی تأثیر ترکیب فولاد ضد زنگ بر خواص مکانیکی است.
- آستنیتی(Austenitic): مقدار کروم، مولیبدن و نیکل در فولادهای زنگ نزن آستنیتی بیشتر است. این گروه داری مقاومت در برابر خوردگی و استحکام است و یک فولاد ضد زنگ تولید می کند که به راحتی خم می شود و شکل می گیرد.
- فریتیک(Ferritic): یکی از عوامل متمایز کننده فولاد ضد زنگ فریتی، مغناطیسی بودن آن است. ترکیب فولاد زنگ نزن فریتی دارای سطوح کروم بالا و سطوح کربن پایین تر است. این باعث مقاومت بیشتر در برابر استرس می شود.
- آستنیتی-فریتی (دوبلکس)(Austenitic-Ferritic (Duplex)): فولادهای ضد زنگ دوبلکس خواص آستنیتی و فریتی را با هم ترکیب می کنند. این امر محافظت فلزات در برابر خوردگی را افزایش می دهد. ترکیب فولادهای ضد زنگ دوبلکس آن را به گزینه ای عالی برای محیط های دریایی تبدیل کرده است. فولادهای دوبلکس مقاومت بالایی در برابر ترک خوردگی کلرید تنشی نشان می دهند که زمانی رخ می دهد که یک محیط خورنده (مانند قرار گرفتن در معرض اقیانوس) با تنش کششی همراه شود. علاوه بر این، اغلب در صنایع نفت و گاز دیده می شود.
- مارتنزیتی(Martensitic): نشانه ترکیبی فولادهای زنگ نزن مارتنزیتی افزایش کربن است. مانند فولادهای فریتی، آنها مغناطیسی هستند. با این حال، افزایش کربن باعث می شود فولادهای مارتنزیتی در برابر خوردگی مقاومت کمتری داشته باشند.
- Precipitation-Hardening: ترکیب فولادهای زنگ نزن سخت شامل 15-17.5٪ کروم و 3-5٪ نیکل است. مقادیر کمی از آلومینیوم، مس و نیوبیم نیز وجود دارد. این ترکیب باعث ایجاد یک فولاد ضد زنگ فوق العاده قوی، بادوام، سخت و مقاوم در برابر خوردگی می شود.
برخی از گریدهای فولاد زنگ نزن آستنیتی کدامند؟
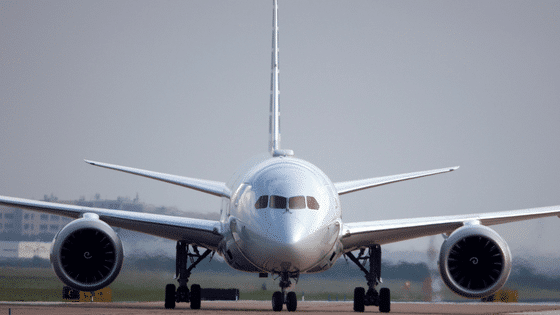
- فولاد ضد زنگ 201 – ترکیب فولاد ضد زنگ 201 شامل کربن، منگنز، فسفر، گوگرد، سیلیکون، نیکل، نیتروژن و 16 تا 18 درصد کروم است. شما احتمالاً آن را در صنعت خدمات غذایی برای مواردی مانند تجهیزات پخت و پز و لوازم تجاری و همچنین صنایع معماری و خودرو مشاهده خواهید کرد. بورس آهن ورق فولادی ضد زنگ 201، ورق فولاد ضد زنگ 201LN، ورق فولاد ضد زنگ 201 و ورق فولاد ضد زنگ 201LN را عرضه می کند.
- فولاد ضد زنگ 301 – ترکیب فولاد زنگ نزن آستنیتی 301 مشابه 201 است که شامل کربن، منگنز، فسفر، گوگرد، سیلیکون، نیکل، نیتروژن و 16-18 درصد کروم است. با این حال، سطح منگنز آن بسیار کمتر و تقریباً دو برابر مقدار نیکل آن نسبت به 201 است. به احتمال زیاد 301 را در اجزای مورد نیاز در صنعت هوافضا مشاهده خواهید کرد.
برخی از گریدهای فولاد ضد زنگ فریتی کدامند؟
- فولاد ضد زنگ 409 – این فولاد ضد زنگ فریتی عمومی دارای محتوای کروم بسیار کمتری نسبت به 201 یا 301 در کمتر از 12 درصد است. تفاوت اصلی اضافه کردن تیتانیوم است. تیتانیوم فولاد را تثبیت می کند و به محافظت عالی در برابر خوردگی در دماهای بالا کمک می کند. یکی از کاربردهای رایج برای سیستم های اگزوز در هر دو صنعت خودرو و کشاورزی است.
- فولاد ضد زنگ 441 – دو تفاوت اصلی در ترکیب شیمیایی بین فولاد ضد زنگ 409 و 441، افزودن نیوبیم و محتوای کروم بسیار زیاد بین 17.5 تا 19.5 درصد است. با هم، این تفاوت ها منجر به یک فولاد ضد زنگ با عملکرد بالا در برابر اکسیداسیون و مقاومت در برابر خوردگی در دماهای بالاتر می شود.
چگونه می دانید کدام ترکیب فولاد ضد زنگ برای پروژه شما بهترین است؟
اکنون که ما آموختیم که دو خانواده مختلف از فولاد ضد زنگ وجود دارد که با ترکیبی از ریزساختار و نسبت عناصر آلیاژی تعیین می شود و دارای تغییرات شیمیایی جزئی تا اصلی هستند، چگونه می دانید که کدام ترکیب فولاد ضد زنگ برای پروژه مناسب است؟
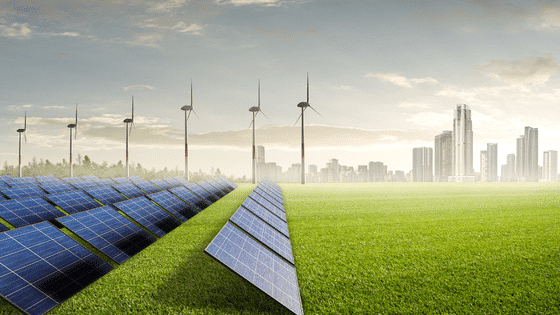
نگران نباشید، هیچ کس از شما انتظار ندارد که یک متخصص متالورژی یا علاقمند به جدول تناوبی شوید. حقیقت این است که هیچ پاسخ یکسانی برای این سوال وجود ندارد.
اما، چند نکته مفید وجود دارد که باید به عنوان راهنما در نظر داشته باشید. شاید نکته اصلی این باشد که در نظر بگیرید چگونه اثرات اولیه عناصر آلیاژی اصلی موجود در ترکیب فولاد ضد زنگ با نیازهای پروژه شما مطابقت دارد.
- کروم (CR): کروم مهمترین سهم عنصری در فولاد ضد زنگ است. به یاد داشته باشید که چگونه می توان یک فولاد را طبقه بندی کرد ضد زنگ باید حداقل 10.5 تا 11 درصد کروم داشته باشد. هنگامی که به ترکیب شیمیایی انواع فولاد ضد زنگ نگاه می کنید، گریدهایی که محتوای کروم بالاتری دارند محافظت بهتری در برابر خوردگی نشان می دهند. بنابراین، سطوح بالاتر کروم را برای محیط های بسیار خورنده، به ویژه در دماهای بالا، در اولویت قرار دهید.
- نیکل (Ni): نیکل مقاومت در برابر خوردگی و استحکام را بهبود می بخشد و شکل پذیری را افزایش می دهد. از بین این سه اثر، با افزایش درصد نیکل موجود در فولاد ضد زنگ، شکل پذیری به طور چشمگیری افزایش می یابد.
- مولیبدن (Mo): مولیبدن مقاومت در برابر خوردگی اتمسفر را افزایش می دهد. به عنوان مثال، فولاد ضد زنگ 316 یکی از محبوبترین گریدها است و در محیطهای شدید دما که باعث زنگ زدگی، سوراخ شدن یا کرنش میشوند، برتری دارد.
- کربن (C): به طور کلی، فولادهای ضد زنگ دارای محتوای کربن بسیار کمتری نسبت به سایر محصولات فولادی هستند که معمولاً کمتر از 2٪ است. با افزایش کربن، مقاومت در برابر خوردگی کاهش می یابد، در حالی که سختی و استحکام ممکن است افزایش یابد.
- نیتروژن (N): حفره زمانی رخ می دهد که فلز در معرض یک محیط خورنده بسیار موضعی قرار گیرد. فلز سوراخ هایی ایجاد می کند که می توانند به شکاف تبدیل شوند. بیشتر پروژهها به محافظت در برابر حفرهها نیاز دارند، و اینجاست که نیتروژن میتواند کمک کند. این عنصر، مقاومت در برابر شکاف و خوردگی بین دانه ای را تا حد زیادی بهبود می بخشد.
- منگنز (Mn): منگنز یک اثر تثبیت کننده دارد، به ویژه زمانی که نیتروژن در ترکیب فولاد ضد زنگ وجود داشته باشد. اثرات دیگر عبارتند از افزایش استحکام کششی و سختی پذیری.
- سیلیکون (Si): سیلیکون یک تثبیت کننده فریت است که اکسید زدایی می کند. اکسیداسیون به مقاومت در برابر خوردگی کمک می کند.
- تیتانیوم (Ti): تیتانیوم همچنین تثبیت را بهبود می بخشد. دو اثر کلیدی که تیتانیوم در فولاد ضد زنگ خواهد داشت، به حداقل رساندن خوردگی بین دانه ای و افزایش جوش پذیری است.
موارد فوق فقط یک راهنما است. اگر مطمئن نیستید که کدام ترکیب فولاد ضد زنگ نیازهای خاص پروژه شما را برآورده می کند، تیم متخصصان بورس آهن آماده کمک هستند.