فولاد ضد زنگ در علم متالورژی، با نام استیل نیز شناخته می شود، این نوع فولاد خانواده بزرگی از انواع فولاد با خاصیت های مکانیکی متفاوت را شامل می شود که نقطه اشتراک آنها وجود حداقل 11% کروم در ترکیب آنها آست.
در واقع این عنصر مهم ترین عنصر آلیاژی و به نوعی همه کاره درفولاد ضد زنگ است. وجود این عنصر برای جلوگیری از وقوع واکنش بین آهن و اکسیژن حیاتی است.
بجز کروم، در گرید های مختلف فولاد ضد زنگ ( استیل ) عناصری مانند
- کربن
- مولیبدن
- نیتروژن
- آلومینیوم
- سیلیسیوم
- فسفر
- گوگرد
- مس
- نیکل
- سلنیوم
- نیوبیوم
نیز وجود دارد. این عناصر با توجه به خاصیت های مکانیکی مورد نیاز محصول نهایی به ترکیب فولاد در هنگام ریخته گری افزوده می شود.
مقاومت در برابر خوردگی در فولاد ضد زنگ حاصل از شکل گیری لایه ای نازک، غیر فعال و چسبنده (passive film) است که بخاطر کروم بر روی سطح آن شکل می گیرد. وجود این لایه غیر فعال و چسبنده، باعث مقاوت فولاد در برابر خوردگی است و حتی در صورت وجود آسیب یا خراش، خود را ترمیم کند.
حتی با برخی تغییرات در ترکیب شیمیایی این آلیاژ می توان میزان این مقاومت را افزایش داد، برای نمونه:
- افزایش میزان درصد کروم در آلیاژ به مقداری بیشتر (بیشتر از 11%)
- افزودن نیکل به ترکیب آلیاژ به مقداری بیش از 8%
- افزودن مولیبدن به ترکیب آلیاژ
از مزایای فولاد ضد زنگ می توان موارد زیر را برشمرد
- مقاومت بالا در برابر زنگ زدن
- هزینه تعمیرات پایین
- سطحی صیقلی و درخشان
- استحکام بالا
خواص بالا باعث شده این نوع فولاد نیاز مصرف بسیاری از صنایع بزرگ و کوچک باشد و رقابت بر سر تولید با کیفیت فولاد ضد زنگ بین کشورهای صنعتی مانند ژاپن، آلمان و هند در جریان باشد.
تولید این محصول نیاز به دانش و فناوری خاصی دارد. امروزه این نوع فولاد به اشکال مختلفی مانند ورق، صفحه، میله، لوله و .. تولید و روانه بازار می شوند.
آشنایی با انواع فولاد ضد زنگ
فولاد ضد زنگ فریتی
فولاد ضد زنگ فریتی، با 10.5 تا 27 درصد کروم و کمتر از 0.5 درصد نیکل در ترکیب فولاد است. ریز ساختار این آن از فاز فریت (α) است که ساختار کریستالی (BCC) دارد. با توجه به درصد بالای کروم، معمولا در دمای متفاوت ساختار کریستالی به همین صورت باقی می ماند.
ساختار BCC خاصیت آهنربایی دارد و می تواند آهنربا را جذب کند. به همین دلیل این فولاد مغناطیسی می گویند.
فولاد ضد زنگ فریتی، قابلیت استحکام بخشی با روش های عملیات حرارتی را ندارد. هم چنین استحکام بخشی با روش سختی نیز تاثیر چندانی در افزایش استحکام آن نخواهد داشت.
فولاد ضد زنگ آستنیتی
فولاد ضد زنگ آستنیتی، با عناصر نیکل، منگنز و کروم ترکیب شده و تشکیل آلیاژ می دهد. بطور معمول فولاد ضد زنگ آستنیتی حدود 16-20 درصد کروم و 7-20 درصد نیکل در ترکیب خوددارد.به همان شکل که قبلا توضیح داده شد نیکل برای پایداری فاز است. به همین دلیل این فولاد در تمامی دما ها از فاز آستنیت با ساختار FCC بر خوزدار است و نیتروژن کمک زیادی به افزایش پایداری فاز آستنیت می کند.
از مزایای نیکل برای فولاد آستنیتی، حفظ استحکام آلیاژ در دمای بالا و مقاومت زیاد در برابر خوردگی آلیاژ است. با توجه به این خاصیت ها از این آلیاژ در ساخت کوره حرارتی، لوله انتقال مواد شیمیایی مثل اسید کریدریک (HCl)، سولوفوریک اسید (H2SO4)، اسید نیتریک (HNO3) و یا مبدل های حرارتی استفاده می شود.
این فولاد فاقد سخت کاری با روش عملیات حرارتی و خاصیت مغناطیسی است.
فولاد ضد زنگ مارتنزیتی
این دسته از، آلیاژی بر اساس کربن و کروم است و در ساختار آن حدود 12-17 درصد کروم وجود دارد. این فولاد در اثر سریع سرد کردن آلیاژ از ناحیه آستنیتی تولید شده و به همین دلیل به فولاد ضد زنگ مارتنزیتی معروف است.
فولاد مارتنزیتی بیشترین درصد کربن را در بین آلیاژ های فولادی ضد زنگ است. وجود این حجم از کربن، باعث ایجاد کاربید کروم در مرزدانه های فولاد شده و این فاز افزایش خوردگی را به دنبال دارد.
به این دلیل فولاد ضد زنگ مارتنزیتی بر خلاف نوع فریتی و آستنیتی مقاومت خوبی در برابر خوردگی ندارد. اما در مقابل، استحکام، سختی، چقرمگی و مقاومت خستگی بالا از نقاط قوت این نوع فولاد است.
بیشتر از این فولاد در موارد زیر استفاده می شود
- ساخت قاشق
- کارد
- فنرها
- فولاد ابزار
در یک جمع بندی کلی می توان فولاد ضد زنگ بالا را به شکل زیر خلاصه کرد
انواع فولاد کروم دار: این دسته از فولاد جزوه اولین های فولاد مارتنزیتی هستد که تولید شده است و هم اکنون نیز بیشترین مصرف را در بین فولاد های ضد زنگ مارتنزیتی دارند. در این دسته، کروم اصلی ترین عنصردر ساخت آلیاژ است. از این فولاد بشتر در مواردی مورد استفاده قرار میگیرد که به مقاومت خزشی بالایی نیاز است،
فولادهای نیکل و کروم دار: مشابه دسته قبل است با این تفاوت که مقداری از کربن کم شده و بجای آن نیکل در ساختار آلیاژ استفاده شده است. این تغییر سبب افزایش چقرمگی و مقاومت به خوردگی در این آلیاژ می شود.کاربرد نمونه ها با درصد نیکل بالا، در توربین است.
فولاد رسوب سخت شونده: در این دسته از فولاد قابلیت رسوب سختی و مارتنزیتی با هم وجود دارد. استحکام و چقرمگی شکست در این آلیاژ مناسب است و صنایع هوایی یکی از کاربرد های شاخص آن است.
فولاد مقاوم خزش: همان طور حدس زده اید، این فولاد مقاومت خزشی بالا دارد و از آن در مواردی که دما بالا است و خزش شدت می گیرد، استفاده می شود. روش تولید این دسته با اضافه کردن مقدار کمی بور، کبالت، وانادیم و نیوبیوم به ترکیب اصلی حاصل می شود.
فولادهای ضد زنگ دوفازی (داپلکس)
این دسته از فولا بخاطر این به دو فازی شهرت دارند که ساختار آن ترکیبی از دو فاز فریت و آستنیت است. این آلیاژ به جهت داشتن کروم و مولیبدن بالا معروف هستند. مقدار کروم در این آلیاژ بین 19-32% و مولیبدن حداکثر 5% است.
از خواص این نوع فولاد مقاومت به خوردگی خوب، استحکام بالا و قیمت مناسب را می توان نام برد. طبق آزمایش های انجام شده، استحکام تسلیم این فولاد تقریبا دو برابر استیل آستنیتی است! مقاومت خوردگی تنشی این فولاد عالی است که به دلیل وجود فاز فریت در ساختار آن است.
خوردگی تنشی (SCC) تحت شرایطی مثل وجود کلریدها، رطوبت یا دمای بالا برای استیل مشکل افرین است. به این دلیل، فولاد آستنیتی 304 و 316 در این شرایط بهتر عمل می کنند. هم چنین به دلیل کاهش مقدار نیکل، هزینه تولید کمتر است.
فولاد ضد زنگ رسوب سخت شونده
گروه فولاد رسوب سخت شونده به خاطر وجود محدودیت در افزایش استحکام فولاد ضد زنگ آستنیتی و فریتی و افزایش چقرمگی در فولاد مارتنزیتی توسعه پیدا کرده اند. بر اساس ریز ساختار، فولادهای رسوب سخت شونده را می توان در 3 دسته زیر قرار داد
- فولاد رسوب سختی مارتنزیتی
- فولاد رسوب سختی نیمه آستنیتی
- فولاد رسوب سختی آستنیتی قرار داد.
فولاد ضد زنگ رسوب سخت شونده مارتنزیتی
فولاد رسوب سختی مارتنزیتی خاصیت سختی بسیار زیادی دارد و بیشتر در قالب سیم، میلگرد، ورق و قطعات سنگین در فرایند فورج، استفاده می شود. این دسته از فولاد در دمای اتاق ساختاری مارتنزیتی دارند.
اما گاهی فریت در ترکیب این آلیاژها مشاهده می شود که با عملیات همگن سازی و طی آستنیته شدن فولاد، می توان این فاز را حذف کرد. پس از تبدیل ساختار به حالت مارتنزیتی، طی عملیات رسوب سختی و با رسوب یک فاز ثانویه در ساختار، می توان سختی را مجددا افزایش داد.
فولاد زنگ نزن رسوب سخت شونده نیمه آستنیتی
این گروه بخاطر این موضوع نیمه آستنیتی نام گرفته است که در حالت آنیل شده ساختار آستنیتی دارد، اما با یک عملیات حرارتی مناسب به مارتنزیت تبدیل می شود.
ساختار مارتنزیتی می تواند به وسیله کوئنچ سریع قطعه یا عملیات کارسرد شدید قطعه شکل گیرد. سپس عملیات پیرسازی در دمای بالا (برای مثال 510 درجه سانتیگراد) باعث رسوب فاز ثانویه و افزایش سختی آلیاژ می شود.
فولاد ضد زنگ رسوب سخت شونده آستنیتی
فولاد آستنیتی در هنگام انجماد ساختار آستنیتی دارد و این ساختار در تمامی دماها پایدار است. این موضوع به دلیل حضور بالای عنصر نیکل در ساختار است که پایدارکننده فاز آستنیت است.
افزایش استحکام در این فولاد توسط عملیات انحلال و پیرسازی انجام می شود. دقت داشته باشید که زمان پیرسازی نسبت به فولاد رسوب سخت شونده مارتنزیتی و نیمه آستنیتی بیشتر است.
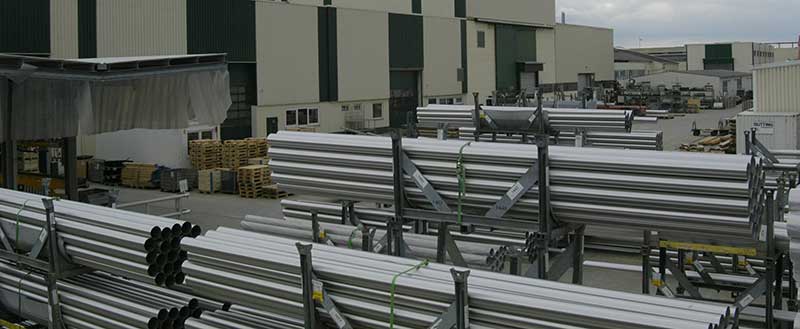
مرحله تا تولید فولاد ضد زنگ
- ذوب مواد اولیه
- کربن زدایی از مذاب
- ریخته گری پیوسته
- شکل دهی
- عملیات حرارتی
- حذف اکسیدهای سطحی
- برشکاری
- تمام کاری
کاربرد های فولاد ضد زنگ
- پرینت 3 بعدی فلزات
- ابزار جنگی
- صنایع شیمیایی و پالایشگاه ها
- معماری و ساختمان سازی
- کاربرد در صنایع هوایی
- ظروف غذا و نوشیدنی
- ساخت وسایل کشاورزی
- تجهیزات پزشکی
- حوزه انرژی
- وسایل زینتی